- „Completely Knocked Down“: Seit 1950 exportiert die Marke Volkswagen Pkw Fahrzeuge in Einzelteilen und setzt sie im Ausland zusammen
- Ziel: Märkte erschließen und globales Volkswagen Produktionsnetz verbinden
- Jährlich rund 25.000 Übersee-Container in zehn Länder und an 27 Standorte
- Bis heute rund 200 Millionen Fahrzeuge exportiert
- High-Tech-Versand mit Robotik und künstlicher Intelligenz
Seit 1950 liefert die Marke Volkswagen Pkw in Einzelteile zerlegte Fahrzeuge ins Ausland, um sie im Zielland zu montieren. Das Verfahren heißt „Completely knocked down (CKD)“ - vollständig zerlegt. Ging es anfangs nur darum, neue Märkte zu erschließen, stellt CKD heute auch die Versorgung des weltweiten Produktionsnetzwerks von Volkswagen sicher - und ist ein wichtiger Umsatzfaktor: Bis heute wurden rund 200 Millionen Fahrzeuge in alle Welt exportiert. Pro Jahr kommen rund drei Millionen Teile oder Fahrzeuge hinzu. Das erste Auto, das in Einzelteilen aus einer Kiste zusammengesetzt wurde, war der legendäre Käfer.
Der Einsatz von CKD kann verschiedene Gründe haben: Fehlende Rentabilität für den Bau einer eigenen Fabrik im betreffenden Land, zu geringe Stückzahlen, hohe Kosten für eine neue Einrüstungen der Produktion vor Ort oder auch Zoll- und Einfuhrbestimmungen.
In Wolfsburg laufen die Fäden zusammen
Und so funktioniert‘s: Alle CKD-Bestellungen der Überseewerke laufen zentral in Wolfsburg zusammen. Dort stellt das Versorgungsmanagement die Verfügbarkeit der Fahrzeugteile bei den europäischen Werken und Lieferanten sicher. Die Fahrzeugteile werden dann in einem der acht Verteilzentren gebündelt, verpackt, in Container geladen und per Schiff, Bahn und Flugzeug nach Übersee und Russland verschickt, wo sie montiert werden. Allein an den Verteil-Standorten Wolfsburg, Salzgitter und Kassel arbeiten 660 Mitarbeiterinnen und Mitarbeiter. Weitere Standorte sind Duisburg, Emden, Fallersleben, Wilhelmshaven und Martorell (Spanien). Diese acht Verpackungsbetriebe liefern jährlich insgesamt rund 1,7 Millionen Kubikmeter Ware aus - was rund 25.000 Übersee-Containern entspricht. Vom Eingang der Bestellung vergehen rund acht Wochen bis das Fahrzeug im Zielland ausgeliefert wird. Insgesamt werden rund 90 verschiedene Fahrzeugprojekten der Überseewerke aus Europa per CKD beliefert.
Zuerst kam der Käfer aus der Kiste
Alles begann 1950, als der erste Käfer in Teilen zerlegt in Irland ankam. Es folgten Lieferungen nach Südafrika, Argentinien, Brasilien und Mexiko. Gerade für Südamerika war die Montage der zerlegten Fahrzeuge auch der Grundstein für die heutigen großen Produktionsgesellschaften, wie beispielsweise Volkswagen do Brasil oder Volkswagen de México. Heute gibt es montierende 27 Standorte in zehn Ländern: Das größte CKD-Montagewerk befindet sich in Südafrika, wo unter anderem der Polo für alle Rechtslenker-Märkte hergestellt wird. Ebenfalls ein Exportschlager ist der Tiguan, welcher per CKD auch in Russland und Mexiko montiert wird. Weitere Standorte sind in den USA, China, Brasilien, Argentinien, Indien, Malaysia und Indonesien.
Von Hand zu High-Tech
Wo früher die Teile händisch in Kisten verpackt wurden, hat heute längst High-Tech Einzug gehalten: Modernste Roboter unterstützen bei der Verladung der Bauteile in den Verpackungsbetrieben. Sie sind hierfür mit einem speziellen Handaufsatz ausgestattet, der die Fahrzeugteile unterschiedlichster Formen und Größen greifen kann. Dadurch wird das Team vor Ort besonders beim Verpacken von schweren Fahrzeugteilen entlastet. Zudem vereinfachen Bots mit Hilfe von künstlicher Intelligenz die E-Mailkommunikation mit Lieferanten. Sie lesen sie quasi mit und reagieren selbstständig: Meldet ein Lieferant beispielsweise auf eine Bestellanfrage per E-Mail, dass eine Charge in mehreren Teillieferungen erfolgen wird, so wird diese Information durch Natural Language Processing (NLP) automatisch erkannt und direkt im SAP-System der Produktionssteuerung hinterlegt.
Burkhard Hüsken, Leiter CKD der Marke Volkswagen Pkw: „Früher hat man die Abstimmung mit den Überseewerken mit ein bis zwei Faxen pro Woche erledigt. Heute agieren wir in Echtzeit mit unseren Produktionswerken und steuern dabei rund 9.000 Teilenummern für den weltweiten Versand. Die Aufgaben der Mitarbeiterinnen und Mitarbeiter haben sich dabei nachhaltig verändert - vom reinen ‚Kisten-Macher‘ hin zum ‚Daten-Logistiker‘.“
Medien
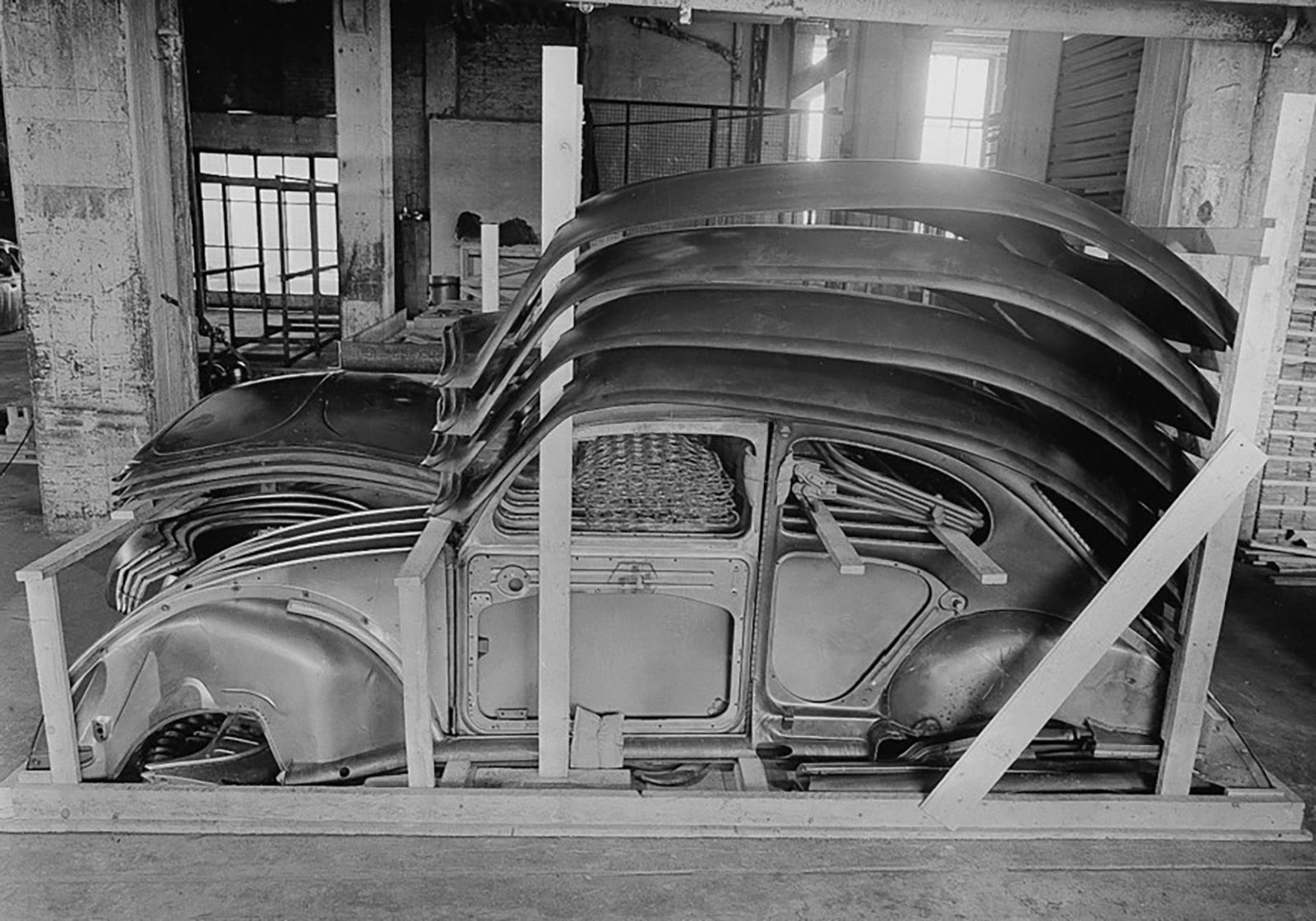

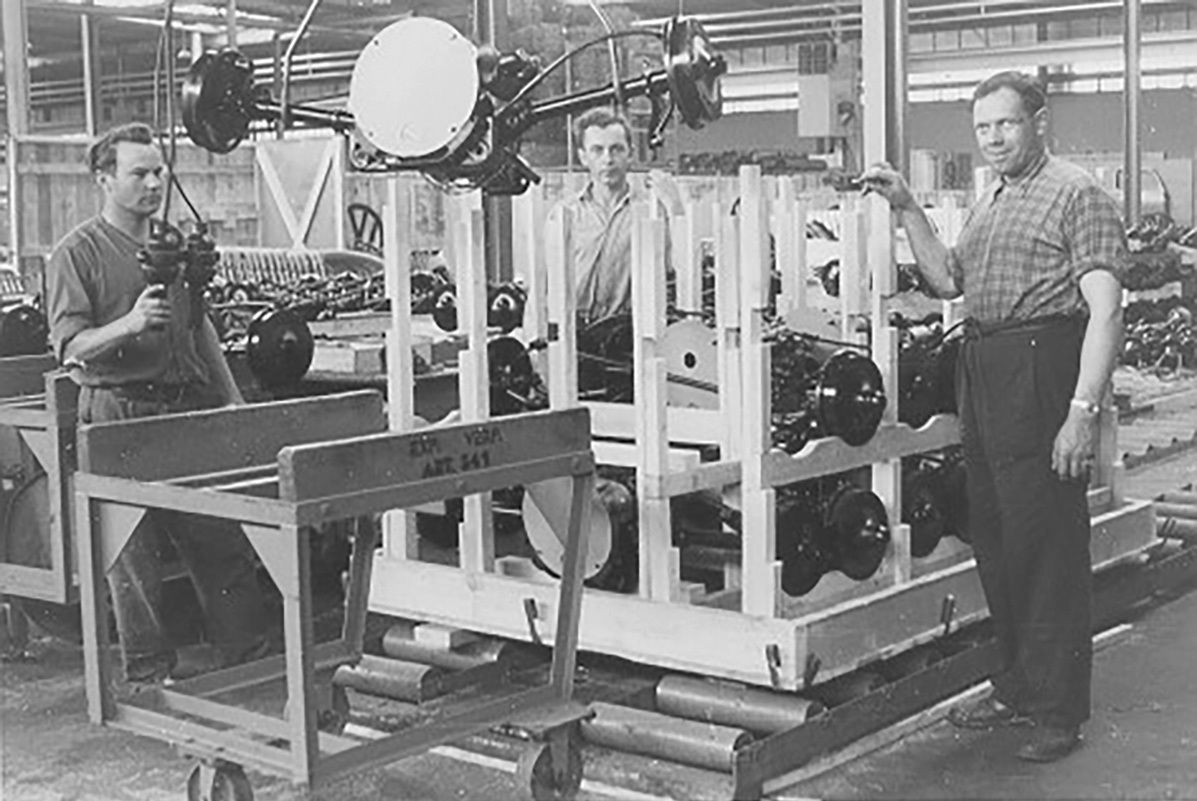
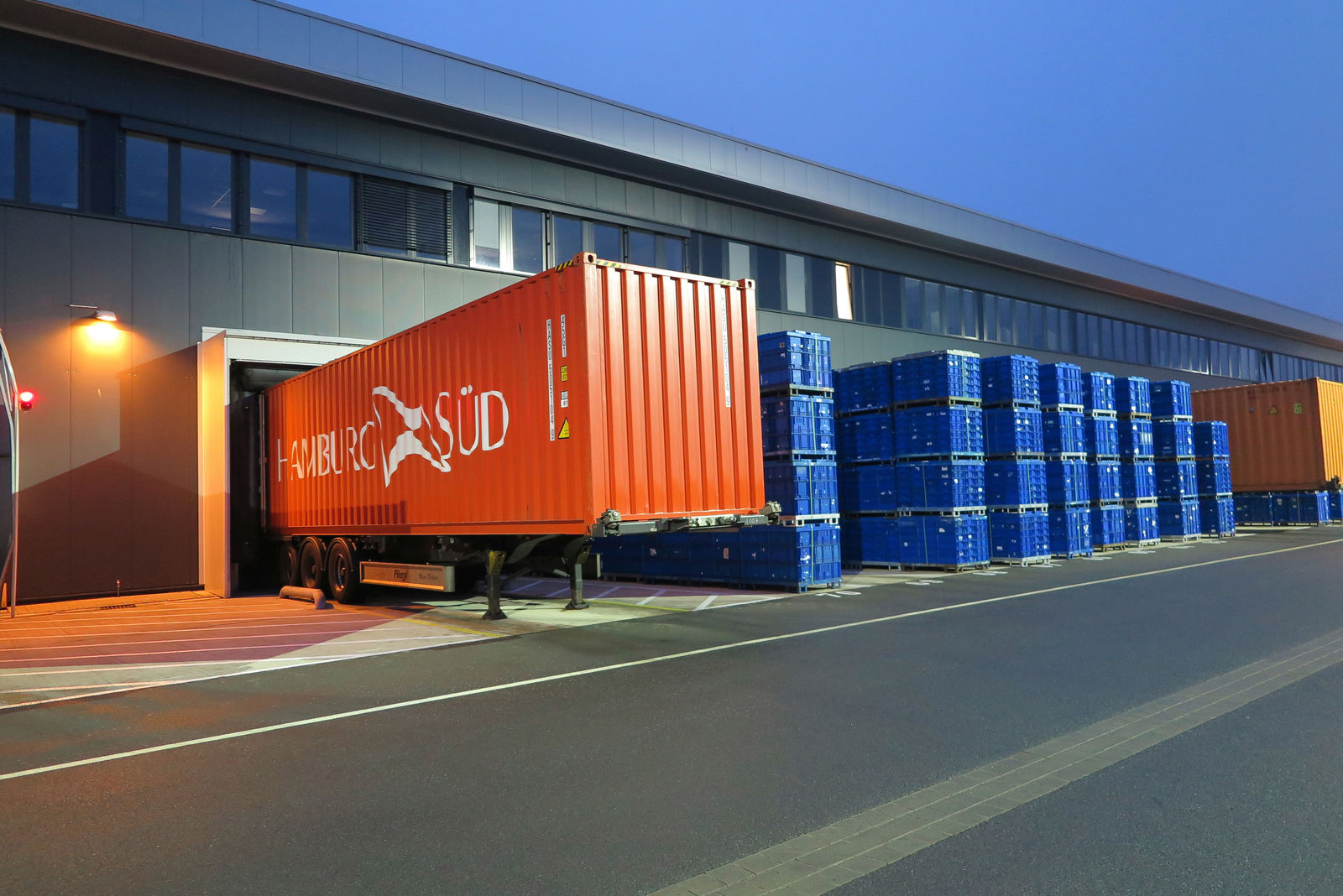
Medienkontakte
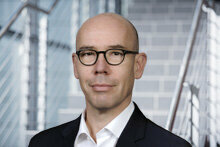
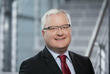