- Productivity improved by more than six percent compared to the previous year - target of an annual five percent increase over all plants exceeded
- In 2019, production will contribute a cost reduction of around 500 million euros with the production strategy TRANSFORM.TOGETHER. Between 2019 and 2023 a total of 2 billion euros will be contributed
- CO2 emissions per vehicle produced will decrease by 22 percent between 2015 and 2019. By 2025, the emissions are to be cut by 50 percent
- Volkswagen board member for production Dr. Andreas Tostmann: “The figures demonstrate that our strategy is working. For the first time since 2013, we lowered the costs per vehicle in production.”
The Volkswagen brand is well on its way to achieving its own goals for more cost-effective vehicle production. Following the launch of the new production strategy TRANSFORM.TOGETHER last year, initial successes are now emerging. Board member for production and logistics Andreas Tostmann commented the interim review with 500 leading managers at an international conference: "The figures demonstrate that our strategy is working. In 2019, our productivity will have improved by more than 6 percent. And for the first time since 2013, we lowered the costs per vehicle in production. The workforce did an extraordinary great job here and I thank them very much for their achievements. We have demonstrated team spirit, and with our new models we managed strong and smooth starts of production. With great competence, our colleagues consistently contribute to increasing production efficiency and productivity. We will continue along our chosen path. Especially in a time of global economic uncertainties, we are well advised to make ourselves crisis-proof. To do what is in our hands so we are prepared for what is not in our hands. "
In total, the production facility costs of the Volkswagen brand amount to around 10 billion euros. Between 2019 to 2023, production is contributing two billion euros to the financial result by reducing personnel costs, procurement incidentals and overhead. In 2019, around 500 million euros will be contributed.
The company is striving to increase productivity across all sites by 30 percent by 2025. Of particular importance to Volkswagen is to bring production facilities with very different conditions all over the world to common production standards. A centralized process ensures that ideas and improvements in one location are quickly and bindingly transferred to other plants. At present, 220 such measures are being implemented. These range from the globally standardized automated surface inspection in the paint shop to the reduced complexity of bodywork press tools to modular special containers that can be used independent of the model.
Enforcing common standards, the new digital production platform developed with Amazon Web Services and Siemens will also help standardize the different IT systems of the individual plants. For example, maintenance requirements of production machinery can be uniformly controlled as part of predictive maintenance. Board member for production Dr. Tostmann explained: "In a large company like Volkswagen, we have to use economies of scale much more consistently. Improvements must be implemented quickly everywhere, and new systems must be developed only once."
On top, the production group at Volkswagen has set itself a comprehensive decarbonization goal. As an intermediate step, the CO2 emissions of the plants are to be reduced by 50 percent by 2025 compared to 2015. The figures from 2015 to the first half of 2019 demonstrate that the company is well on track. CO2 emissions per vehicle produced were reduced by 22 percent.
Media contacts
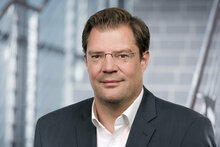
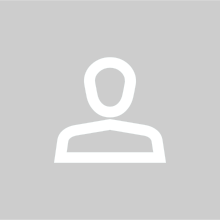